Tips & Facts
- Home
- Tips & Facts
OVERVIEW
Controlling Water Hardness
The phosphate cycle is based upon the principle of precipitating the calcium and magnesium hardness with phosphate. Once the hardness/phosphate precipitate is formed, it also is conditioned as sludge through the use of synthetic or natural polymers. In this physical reaction, many calcium phosphate molecules attach to one polymer molecule and drop as fluid sludge to the bottom of the boiler, where they can be blown down. According to guidelines, the boiler water’s level of pH must be maintained above 9.5 to ensure that the proper chemical reaction occurs between the calcium and magnesium ions and the phosphate molecules. Should unexpected hardness result, a phosphate residual should be maintained. However, there is a major disadvantage to using a phosphate to precipitate hardness. Magnesium phosphate forms a very sticky sludge, and frequently the sludge drops onto the heat transfer surfaces and forms deposits.
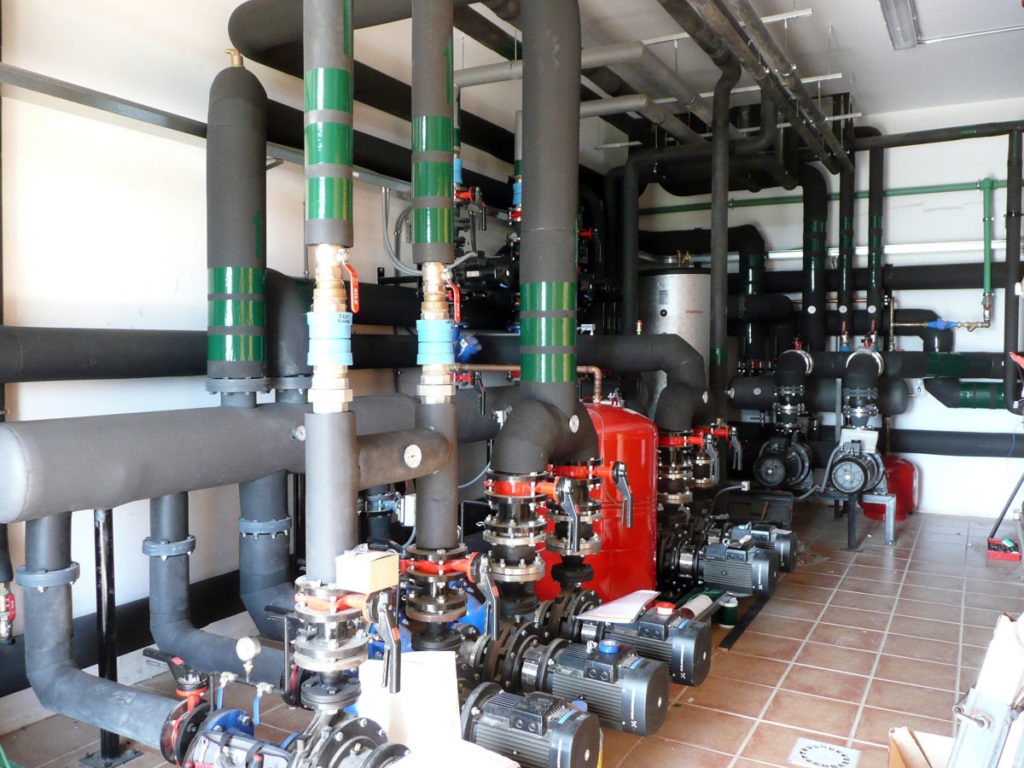
FEATURED
Sludge Conditioning
When hardness is controlled through carbonate and phosphate programs, the resulting sludge must be conditioned into a fluid substance for ease in bottom blowdown. Sludge conditioners generally are very long synthetic or natural chains of polymeric molecules. The sludge conditioner physically bonds with the calcium carbonate or phosphate formed in the boiler to prevent the formation of precipitated scale on the heat transfer surfaces. Several of the most popular internal boiler sludge conditioners are sodium polycrylate, lignin, sodium polymethacrylate, and sulfonated copolymers. It is important to remember that an effective bottom blowdown schedule must be maintained to ensure that the conditioned sludge is removed from the boiler.
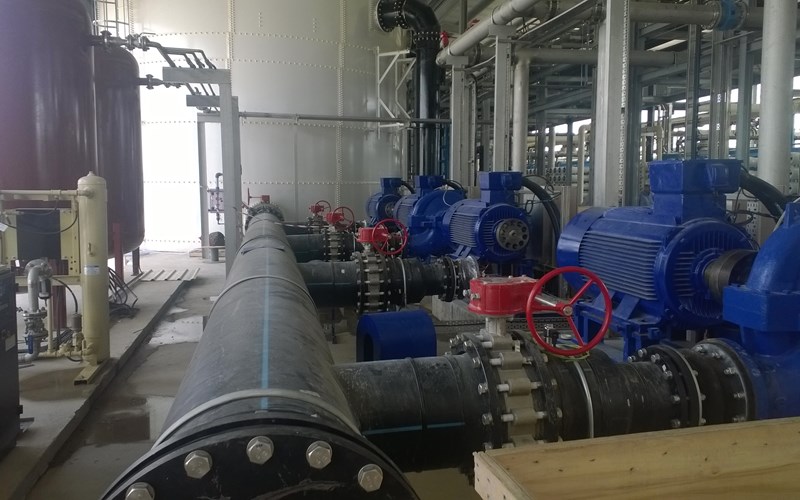
Controlling Alkalinity
Alkalinity control is vital to the success of any internal boiler treatment program. Alkalinity in a boiler system protects the unit against attack and maintains the proper pH level for the necessary chemical reactions to occur. Just as importantly, alkalinity provides hydroxyl ions, which form an insoluble ferrous hydroxide film on metal. The level of alkalinity required in a boiler system depends upon several factors. Most often, however, the level of alkalinity is related to the operating pressure of the boiler. Table 1 shows the relationship between boiler pressure and alkalinity levels in a typical firetube boiler without process restrictions on steam purity. In situations where the calcium and magnesium hardness has been removed mechanically through the use of a sodium exchange softener, alkalinity control can be achieved without the addition of chemical alkalinity builders. A feedwater analysis will show whether proper alkalinity can be achieved without the use of supplemental chemicals.
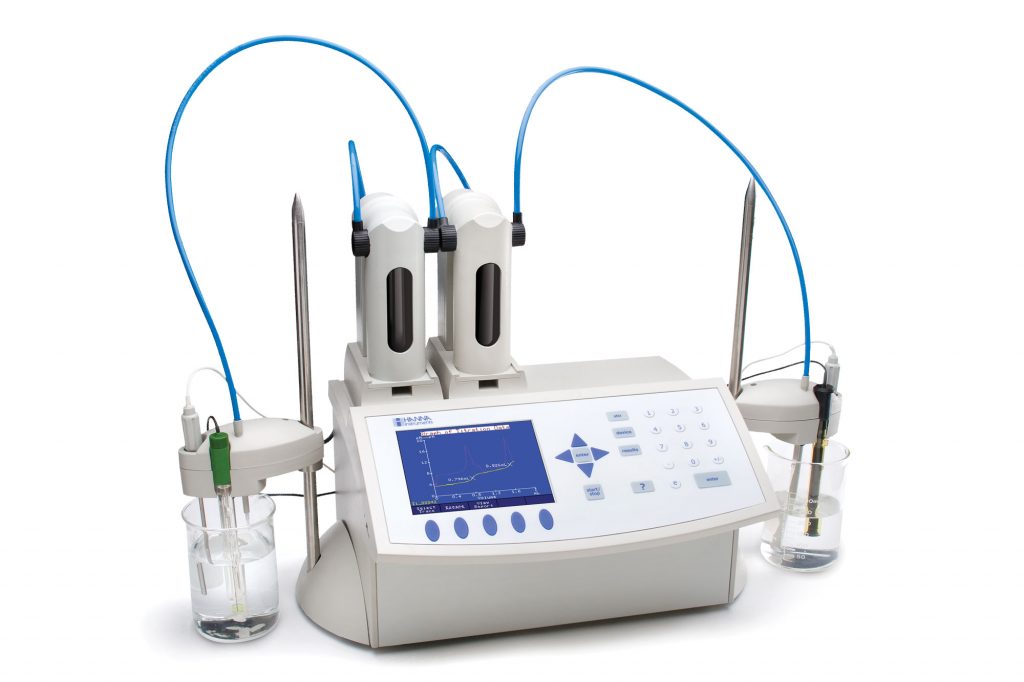
Effective Water Treatment
Your vendor should have a thorough understanding of your heating, cooling, and process needs; how your system functions; and how to maintain clean heat transfer surfaces. Some of the services you should expect to receive include:
- Training of personnel in the day to day maintenance, testing, and operation of your water treatment program.
- Periodic inspections to test and adjust, if necessary, all system parameters.
- Checks of pretreatment equipment and control equipment
- Written recommendations and assessments following each visit.
- An inventory of your chemical treatment products.
- And, most importantly, a knowledgeable water treatment specialist should be able to assist you in ways to reduce energy consumption. boost efficiency, and increase uptime
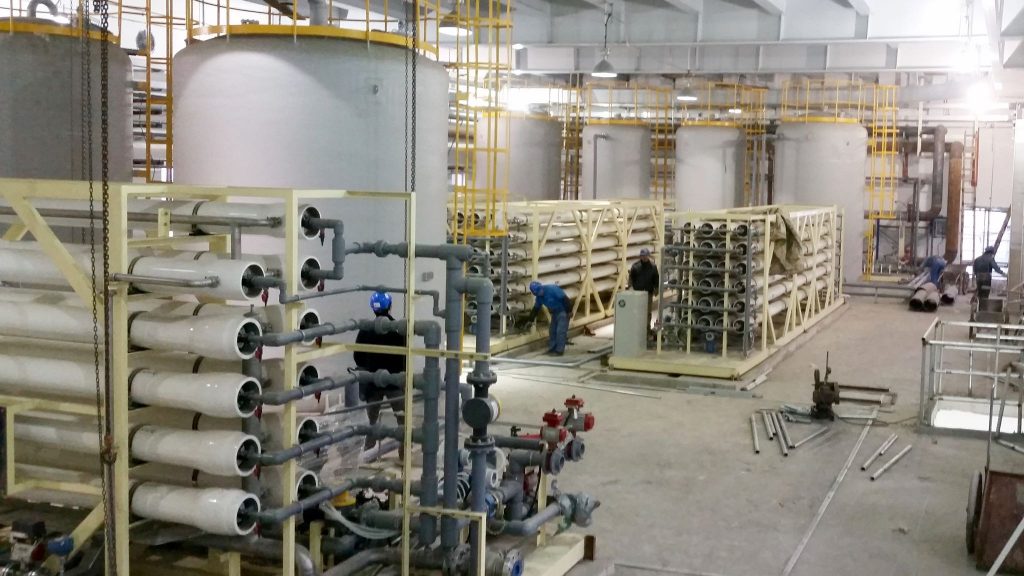
Controlling Dissolved Gases
When dissolved in natural water, carbon dioxide and oxygen greatly increase corrosion. Given boiler system temperatures, even small amounts of oxygen can cause severe damage in the form of pitting. Removal of oxygen, carbon dioxide, and other noncondensible gases from boiler feedwater is vital to boiler equipment longevity as well as safety. The term given to the mechanical removal of dissolved gases is deaeration. Mechanical deaeration to remove the dissolved gases typically is applied prior to the addition of chemical oxygen scavengers. Mechanical deaeration is based on Charles’s and Henry’s laws of physics. Simply stated, the removal of oxygen and carbon dioxide can be accomplished by heating the boiler feedwater and reducing the concentration of oxygen and carbon dioxide in the atmosphere surrounding the feedwater. The best way to accomplish deaeration is to force gas, devoid of 02 and CO2, counterflow to the feedwater. The scrubbing action releases oxygen and carbon dioxide gases that are then vented from the system. In boiler systems, steam is used to”scrub” the feedwater because it’s readily available and adds the heat needed to complete the reaction. For efficient operation, a deaerator must satisfy the following requirements:
Heating of the feedwater. The operating temperature in the unit should be 227 F at 5 psi. The pressure/temperature relationship is important since deaeration must occur rapidly for quick and efficient removal of gases.
Agitation. Agitation is required to decrease the time and heat energy necessary to remove dissolved gases from the water.
Maximization of surface area. The water must be finely dispersed to expose the maximum surface area to the steam. This enables the water to be heated to saturation temperature more quickly and reduces the distance the gases have to travel to be liberated.
Venting. The liberated gases must be allowed to escape from the system as they are released
The two most common chemicals used to remove dissolved oxygen internally are sodium sulfite and hydrazine. Sodium sulfite reacts with oxygen as follows: 2Na2SO3 + 02 2NaSO4. In general, it takes approximately 10 ppm of sulfite as SO3 to scavenge 1 ppm of dissolved oxygen. Hydrazine reacts with dissolved oxygen as follows: N2H2 + 02 2H20 + N2. Theoretically, it takes 1 ppm of hydrazine to scavenge1 ppm of dissolved oxygen and control equipment-able water treatment specialist should be able to assist you in ways to reduce energy consumption. boost efficiency, and increase uptime. Sodium sulfite and hydrazine should be fed to the feedwater line as far back from the boiler as possible. If deaerating heating is utilized, it is advisable to feed the chemical directly to the storage section.
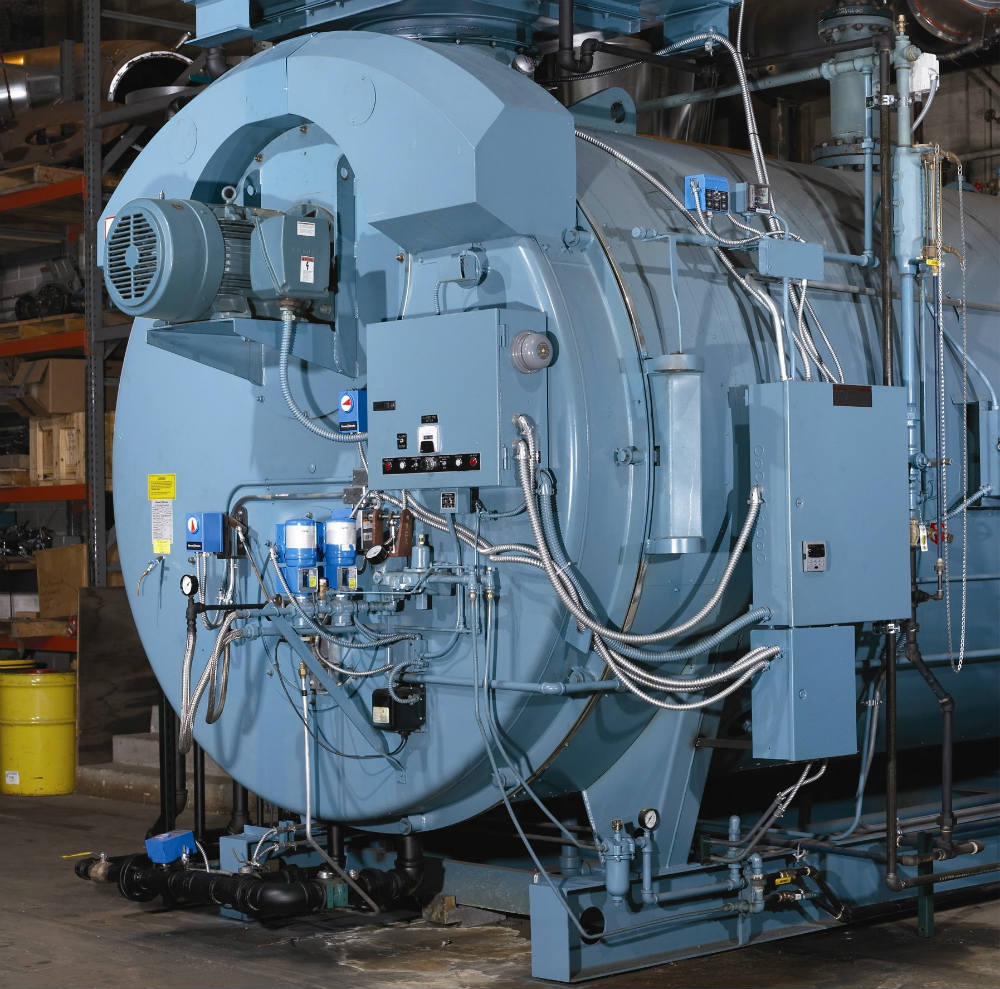